- Home
- 物流ロボット運用最適化のカギはロボット…じゃない!
物流ロボット運用最適化のカギはロボット…じゃない!
物流ジャーナリスト・キクタの連載コラム
<あるある! 物流カン違い>物流分野に漂う22の勘違いを正す!
(2024.11.15)
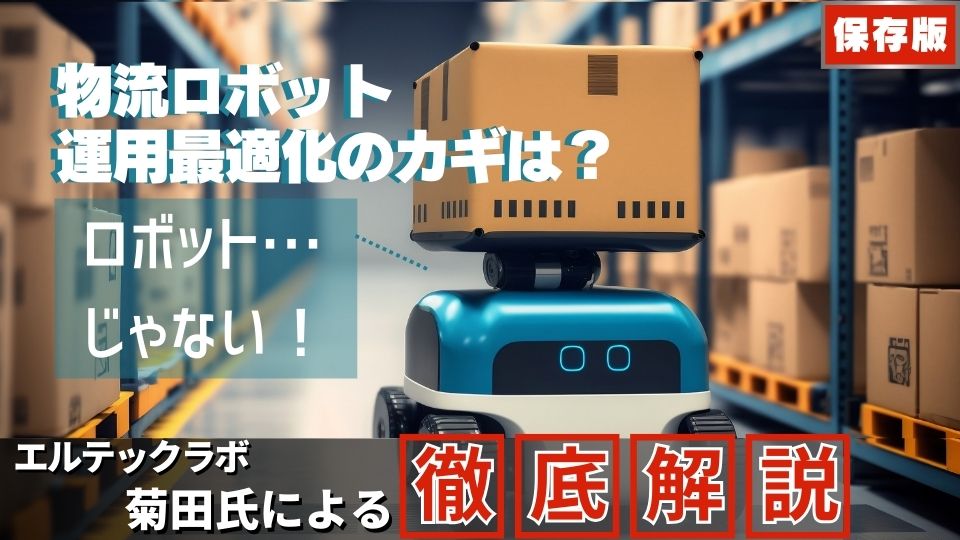
◆現場の生産性向上がマストな時代
物流現場での人手不足傾向が日々強まる中、「より少ない人数で同等以上の仕事ができる、生産性向上」対策が、不可避の課題になっている。漫然と昭和のままのアナログ作業、手仕事を続けようとしても、その「手」が足りなければ、もはや事業継続はおぼつかない。ソフトウェア・ハードウェアの活用で、何らかの省力化・自動化を進める必要がありそうだ。
「…んなこといったって……先立つものがないんだよ!」
皆さん、今でもそうおっしゃるのだろうか? いやまあ、それで仕事を続けられるのなら、とりあえずは結構なことだ(あと数年、「オレの代で畳むんだから!」とかであれば)。ただしその場合、中長期的には持続可能性を失う覚悟が必要になるかも知れない。
生産性向上以前に、人を確保し、定着してもらうために筆者のおススメするのが、前回コラム で述べた「心理的安全性の構築」であった。
◆物流ロボットの種類
「物流ロボット」を大別すると、「ハンドリング」ロボットと「搬送」ロボットがある。ハンドリングロボットは、直角座標型または直角多関節型でアームを持つ機種。基本的には床面等に固定され(AGV/AMRに搭載し走行可能な用例も一部ある)、アームを伸縮・回転させてパレットへのケース品のパレタイズ・デパレタイズ、またはケース・ピース単位のピッキング作業を自動化する。
一方、「搬送」ロボットには次のような機種がある(キクタ式整理)。
①AGV(Automatic Guided Vehicle)
この半世紀来、当たり前に「無人搬送車」と呼ばれてきた。その名の通り、埋設式の磁気ワイヤ、床に貼る反射テープやコード表示、柱や壁に貼るレーザリフレクタなど、誘導媒体のガイドを得て走行するタイプ。各種パレット、直立棚、ケース/プラコン単位で搬送する。
*棚搬送GTPロボットも一般にはAGVである。GTP:Goods To Personとはモノが機械で運ばれ人までやってくること。従来のフォークリフトやカートによるピッキング作業では、人がモノの場所まで取りに行っていた(PTG:Person To Goods)のと逆になる(写真1、2)。
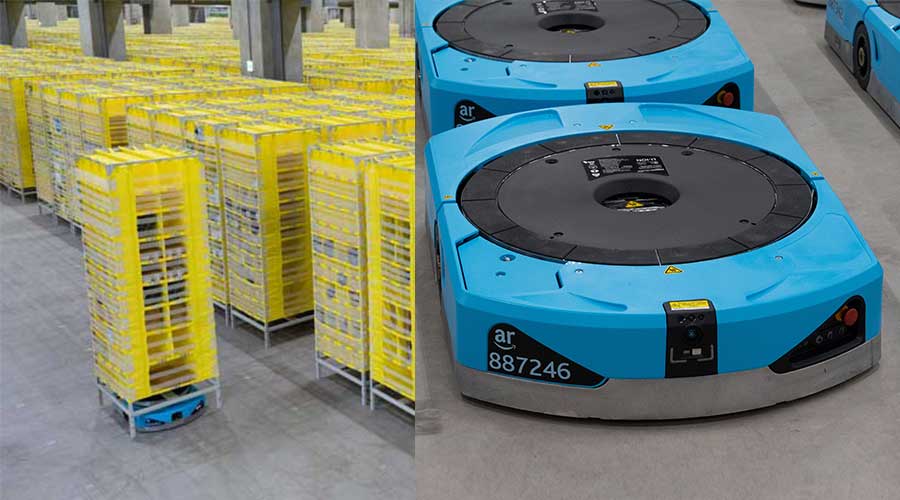
写真1、2 GTPロボットの例/アマゾン川崎フルフィルメントセンターにて(AMAZON Newsroomより)
②AMR(Autonomous Mobile Robot)
自律型走行・搬送ロボット。主に赤外線センサ、カメラなどで自ら周辺環境を3D捕捉しデジタルマップを作成、自己位置を推定しながら移動するSLAM方式により、ガイドレスで自律走行と障害物回避を実現。通常はケース/プラコン単位の搬送を担う(写真3)。なお、従来はAGVとして稼働してきた無人フォークリフトが最近AMRに進化しつつあり、今後の活躍が期待されている。
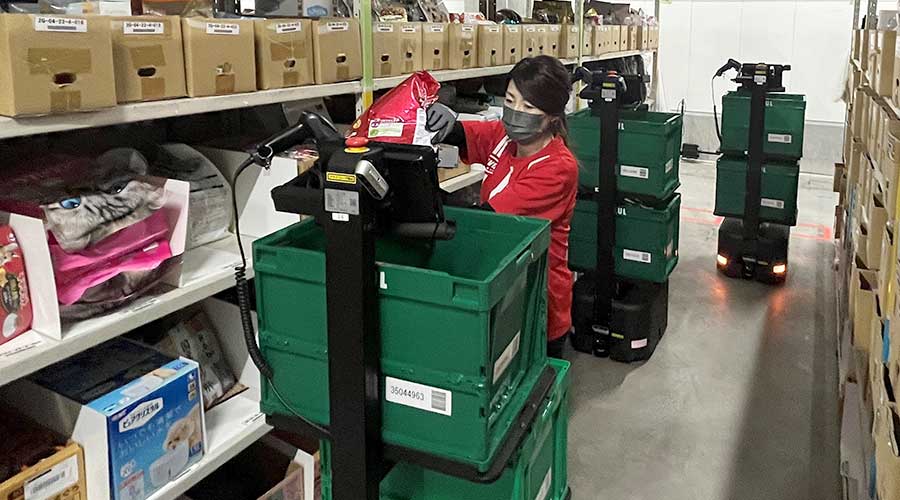
写真3 AMRの導入例(アスクル日高AVC、ラピュタロボティクス製/同社ニュースリリースより)
③シャトルロボット
ロボット式自動倉庫や立体ロボット仕分け機で活躍。機器内でレールに沿って走行しコンテナ単位の入出庫や、リフタで垂直移動し小物品の自動仕分けを行うタイプと、シャトルロボット自体が垂直移動や庫外でのAMR自律走行機能まで合わせ持つタイプ(写真4、5)がある。
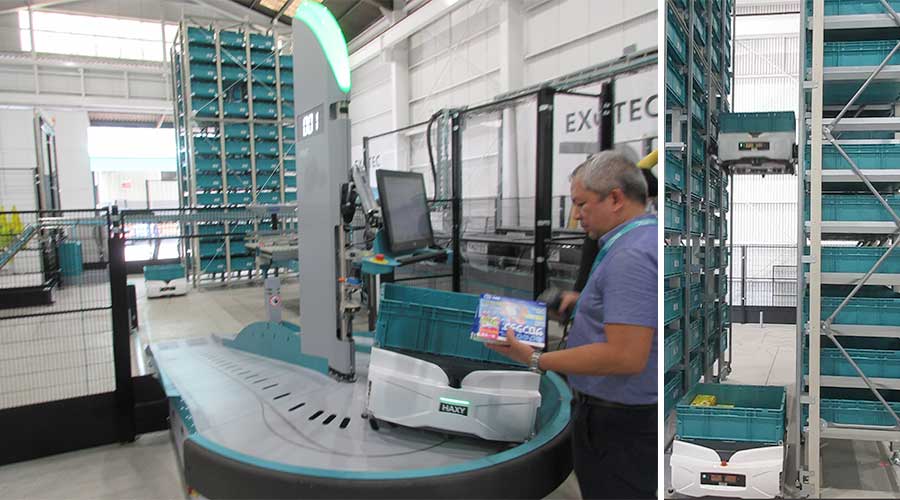
写真4、5 昇降シャトルロボットの例/EXOTEC社のSkyPod(同社日本法人のショールームで筆者撮影)
◆物流ロボットの運用最適化の第1のカギは?-変化への対応
以上の物流ロボットは近年、急速な進化を遂げてきた。従来のマテハンシステム、とくに自動倉庫や自動仕分け機は大型固定設備となることが多く、大規模な投資と工事を必要とするため、中小の現場が簡単に導入できるものは限られた。それに対し物流ロボット――中でも以下は「搬送」ロボットに絞って述べるが――は、大型マテハンに比べ、比較的orかなりor非常に、低コストで導入できるタイプが揃っている。初期投資不要なサブスクサービスも登場しているので、中小の現場でもさほどムリなく採用できそうだ。
だから、物流業務の持続可能化のため、ぜひ導入検討をおススメしたい――ということが1つ。
もう1つ、ぜひともお伝えしたいのが今回のテーマ、「物流ロボットの運用最適化のカギは何なのか?」についてである。
「そりゃ当然、現場に合った、いいロボットを選ぶこと、でしょ?」
――そう思われるのも、ムリはない。だが私は、あえて「ブ~!」とブザーを鳴らしたい。これも、「あるあるカン違い」なのである
もちろん、適切なロボット選びは大切に決まっている。取扱品のアイテム数とサイズ、オーダーあたり出荷数、仕分け口数、前後工程とのバランス……数々のデータ特性から最適な機種を吟味し選択せねばならない。だがそれは「導入」段階の問題だ。私が言うのは、導入した後の「運用」段階の話である。
ロボットの運用で一番の問題になるのは、「変化への対応」ではないかと私は思うのだ。とくに敏感なEC物流を考えれば分かる通り、オーダーの質と量は日次、週次、月次と目まぐるしく変化する。曜日・季節波動は当然として、地域ごとの日々の気候変化(災害含む)、自社キャンペーンのタイミング、他社競合製品の売れ行き、バズリ・ディスリの発生状況……変化要因は山ほどある。これらによって注文内容は七変化し、初期設定のままでは適切に対応できない。
せっかく選んだ物流ロボットが日々、より高い効率で稼働できるようにする――つまりロボットと人の稼働率を最大化し、稼働しない手待ち時間を最小化する――ためには、現場を変化に対応させねばならないのだ。ではその方策は?
◆稼働率最大化・手待ち最小化の施策
第2層に深掘りしたそのカギは、「商品とロボットのロケーション最適化メンテナンスの励行」とまとめて言えるかと思う。
棚搬送ロボットなら、棚に入れる在庫品と、棚じたいを置く保管ロケーションの最適化。そもそも、その棚にどの商品とどの商品をいくつ積み合わせ、どこに置くのか。今の売れ筋商品なら、多めの棚に分散させないと、他のピッキングステーションで待ちが発生する。その棚もステーション近くに置かないと、不要な往復搬送距離が生じ、作業者の手待ちにつながる。ロングテール品なら、出庫作業前に注文の入った複数アイテムを1つの棚にまとめて準備しておければ、遠路はるばるやってきたこのAGVから1個、別のAGVがまた遠くから来て1個、なんていう非効率な仕事を回避できる。
またピッキングステーション側に割り付ける出庫オーダーも、中身によって適度に分散させないと、あるステーションばかりにAGVがやってきて渋滞することでAGVの手待ちが、他のステーションにAGVが来ないことで作業者の手待ちが、発生する。
ピッキング支援AMRなら、ラックに配置する在庫商品のロケーションだ。時々の売れ筋品を適度に分散させ、出庫ラインに近い場所・取りやすい棚位置に置く。各作業者に/AMRに割り付けるオーダーも、偏らぬようバランスよく分散させないといけない。
そして以上について、可能な限り高い頻度で最適化メンテナンスを行うことだ。筆者がこの文脈でいつも紹介している化粧品他のEC企業、オルビスの東日本流通センターの事例では、センター長が「週次以上の頻度で棚在庫ロケーションのメンテナンスをしてます」と語っていた。
こうした変化対応努力を忘れたのか、せっかく導入したロボットが期待効果を出せず、「なんだ、使い物にならんじゃないか!」とお怒りのユーザーもあるかの声を聞く。もしかしたらそれは、ロボットのせいではなく、あなたのせいかも知れない。
そんなざんねんなロボット導入現場には、何が足りていないのか? さらに奥の第3層まで突き詰めると……こうなるのではないかと私は思う。
◆その決め手は、「人の決意と執念」
ロボット運用最適化の要諦は、前項の通り「月々、日々に目まぐるしく変化するオーダーの質と量」を常にウォッチし、追随し、メンテナンスを励行することに尽きる。だが、これはなかなかに大変なことである。もちろん高精度の需要予測データを組み込むことで、ある程度は楽になるだろう(前期オルビス社も最近、AI需要予測システムを導入した)。
それでも完璧な需要予測は現実的に困難だ。管理者、物流現場リーダーは市場動向の変化に日々、耳目をそばだて、地道にデータを収集し、解釈し、物理的メンテナンスを実行し続けなければならない。執念と努力の継続。「絶対に、ロボット導入を成功させるんだ!」という決意と覚悟――よって結論、最後のカギは、ロボットというテクニカルかつハードな次元をはるかに超えた、下記となる。
↓ ↓ ↓ ↓ ↓ ↓
「物流ロボットの運用最適化への最後のカギは、ロボットでなく、<人の決意と執念>である!」
私はそう考えるのだが、いかがであろうか?
(参照文献)菊田、鈴与シンワート連載コラム「物流ムーンショット」、<MoonShots-4>物流ロボットの力を全開!、https://logistics.shinwart.co.jp/column/logistic_it_consultation/kikuta04/ 。
(おしまい)
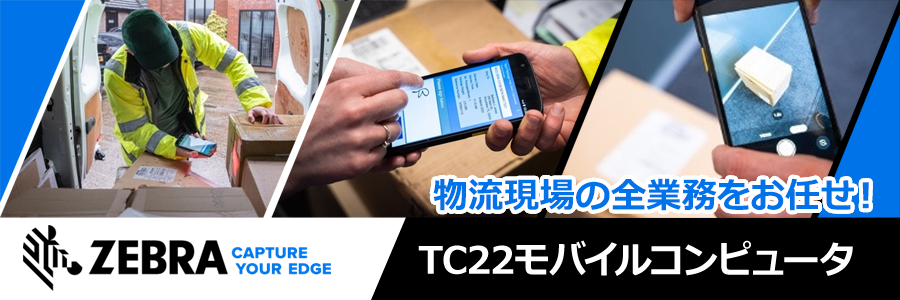
【Androidでドライバーの業務管理をDX化】
オカベマーキングシステムではドライバーの業務管理を円滑にする
業務用スマートフォン・タブレットなどのAndroidデバイスを販売しています。
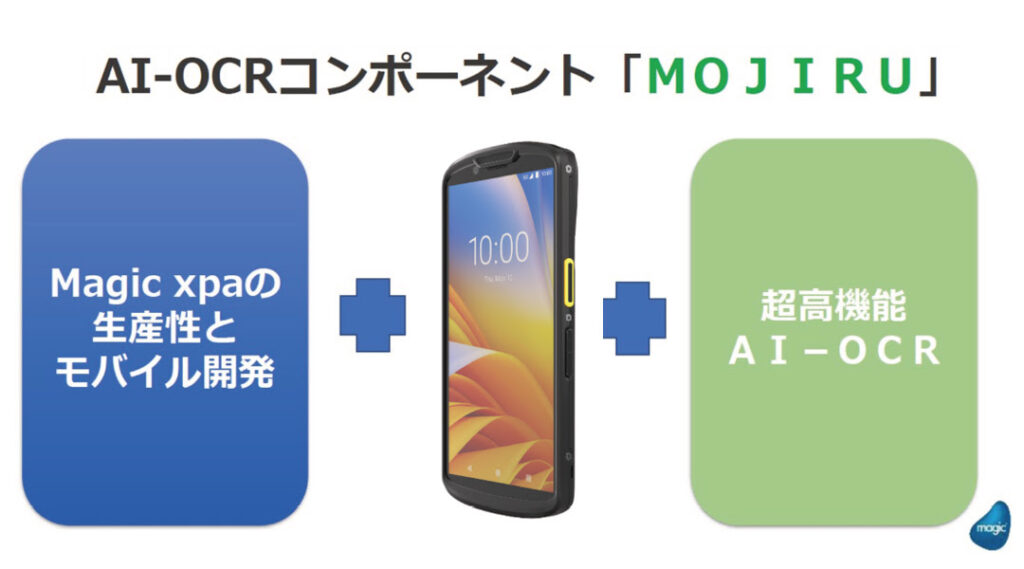