- Home
- 「ノー検品」化なんて、ムリ?~ASNでできること~
「ノー検品」化なんて、ムリ?~ASNでできること~
物流ジャーナリスト・キクタの連載コラム<あるある! 物流カン違い>物流分野に漂う22の勘違いを正す!
(2025.4.15)
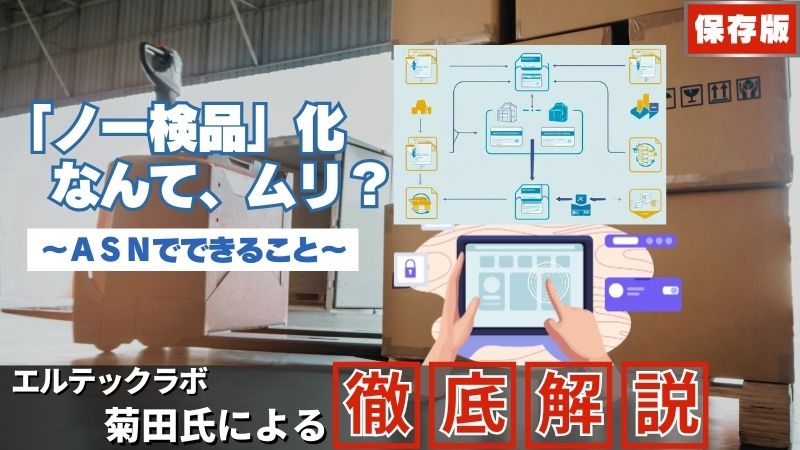
◆七面倒! 悲しい検品作業
改正物流効率化法(物効法)で「荷待ち・荷役等時間の短縮」が発着荷主と物流企業の義務/努力義務化されたことで、物流に係わるすべての企業に、<時間短縮=荷役・荷待ち時間を合わせて「1か所で1時間以内」>遵守への早急な対応が求められている。ドライバーを無為に待たせ、あるいは余計な作業をさせるほど稼働可能時間が減り、「運べない」物流危機を招く恐れがあるからだ。今月(2025年4月)からいよいよ物効法が施行されるタイミングに合わせ数回にわたり、本テーマに関連する「あるあるカン違い」を取り上げることにしたい。
まずは、夢の「ノー検品」化である。検品作業に要する時間は「荷役等時間」に含まれる。それをなくしてしまえれば、こんなに有り難いことはないのだが…
「……んなこと、夢物語。ムリに決まってんじゃん!」
と決めつけてはおられないだろうか? それが実は、カン違いなのである。
着荷主は自分が発注した商品がちゃんと注文通り届いたのか確認し、過不足があれば伝票を修正させねばならないから、何らかの検品作業が荷受け時に行われている。現場が昭和以来の悲しい仕組みのままなら、紙の伝票と実物(品種と数量、賞味期限等)を逐一目視で照合し、伝票にペンでチェックしていく……なんていう七面倒な、とんでもなく手間と時間のかかる作業になるだろう。しかもこうした付帯作業を納品ドライバーに、作業料も払わず、強要していた荷主もあった。従来は「普通」と考えられてきたそんな悪しき商慣行が今や、物流危機を招く原因の1つとして糾弾される時代へと、世は変化した。
伝票と現物の目視照合から一歩進んで、バーコード検品を行っている現場が今では主流だろう。段ボールケースや単品に印字されたITF/JANコードを品種ごとに読み取っては、数量を「いち、に、さん……」と数えて照合し、紙伝票を消し込んでいく。品種間違いの危険は大きく削減されるものの、品種数・個数が多いほど、なおも手数を要する作業になる。
さらに進んでペーパーレス化を達成し、紙伝票ではなくタブレットやスマホ画面のデータで消し込み作業が可能になれば、これはもう、かなり楽になる。それでも品種の数だけ、商品バーコードをスキャンする作業は残る。賞味期限情報はデジタル化されていない場合も多いから、照合・入力の手作業・目視作業も残る。バーコード化はされても、受発注=納品の多品種少量化が進展するなか、ドライバーの負荷と荷役等時間の長さは依然として課題だった。
◆「10万分の1」の精度に検品は必要か
「けど、何で納品の時にもまた、検品を繰り返さなきゃいけないの?」
……こんな声が皆さんの耳元にも届いているだろうか?
発荷主のメーカーは商品を出荷する際、①ピッキング・品揃え時、②ドライバーによるトラックへの積み込み時と、通常は出荷するまでに2回以上検品している。そして誠実なわが日本のメーカー企業の出荷精度は、業界で事情は異なるだろうが、一般的には「10万分の1」程度という、世界トップレベルに到達しているのではないかと思う。ある医薬品卸業ではコスト負担力が高いので超高度なシステムを作り、「100万分の1」、つまりPPMレベルに出荷精度を高めた。これにより顧客の了解を得て、梱包時に封印したボックスの納品時には、「完全ノー検品」化を実現している。また同社は並行して、出荷オリコンに貼付したRFIDのタグに、コンテナ内の出荷品の明細データを書き込み(または紐付けし)、入出荷時にゲートリーダに通してタグ情報を電波で読み取るだけで、実績データ取得・検品照合が可能な仕組みにしている。
そこまでは行かずとも、「10万分の1」レベルの精度が出せているなら、文字通り「10」万が一の差異には目くじら立てず、許容した方が発着双方のコスト安・時短になるのではないか。本項冒頭のボヤキは、そんなメーカーの物流担当者が以前からつぶやいていた言葉である。
とはいえ、所有権の移転を伴う重要な受渡取引業務である以上、何らかの信頼できるエビデンスが欲しい、という受荷主の事情も分かる。そこで以上のトレードオフ問題を解決するため、長年の試行錯誤と検証作業を経て近年、ようやく先進企業が実導入を開始した検品効率化の切り札が、「ASN(Advanced Shipping Notice、事前出荷情報)による納品時の検品レス化」なのである。
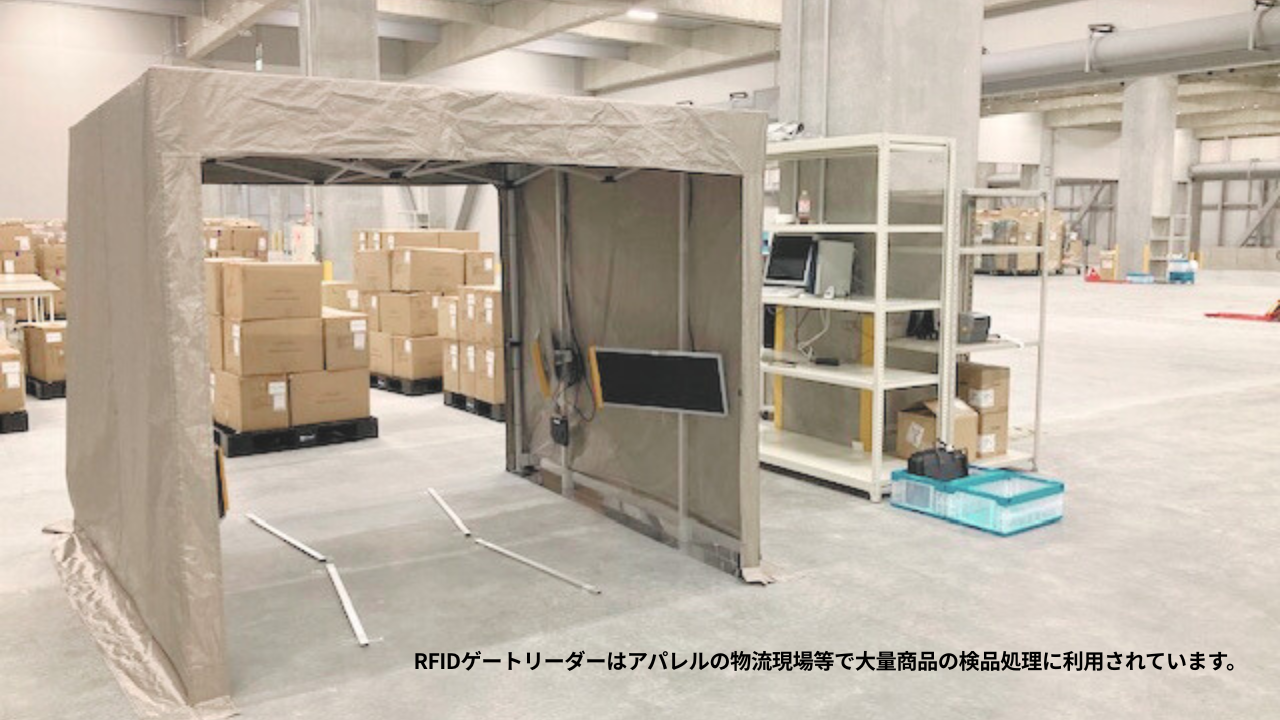
◆ASNでノー検品or簡素化、時短化
この仕組みの概要と注意点を見ておこう。まず納品に先立って発荷主が、顧客から送信されてきた確定発注情報をもとに、納品情報となるASNデータを作り、得意先に送っておく。確定情報でのピッキング後、実際にトラックが着荷主拠点に到着し納品する際、このASN情報を活用することで、検品を大幅に簡素化、ないし不要に=ノー検品化できる、というものである。
ただし、その導入・活用に当たっては、注意点がいくつかある。
まず、ASNの作成には一定の時間がかかるので、加工食品業界などで従来、当たり前に実施されてきた「翌日納品」のままでは、とても時間が足りず、不可能だ。卸・小売側からの確定発注情報の送信タイミングも同じく、ASN作成の可否を左右する。したがって物効法でも奨励されている「納品リードタイム延長」とセットで、発着荷主と物流が連携しながら、導入を進める必要があるのだ。
なので基本、メーカーから顧客への「翌々日納品」化がASN導入の前提条件になるだろう。この点、今や長年にわたって努力が続けられてきた「製・配・販連携」がようやく「販」にまで届き、スーパーマーケット業界などがサプライチェーンの全体最適化に向け、リードタイム延長に応じるようになってきた。つまり、ASN導入の基本条件が整ってきたので、多くの企業にとってチャンスが広がっているのではないかと私は思う。
もう1つの注意点だが、メーカー倉庫からの出荷時に、予測でなく確定情報でピッキングし、トラックに積み込んだ現物とデータを一致させ、ASNにつなぐシステムを構築するのは、かなり難易度が高いということだ。中小規模事業者では対応できないケースも多く、ある加工食品メーカーの場合、物流子会社の専用システムを関連企業にも開放し、ASN化を展開している。
最後に、ASNには一般に、「松・竹・梅」の異なるレベルがあること。つまり①納品単位か、②トラック1車単位か、③パレット単位か――の3段階である。当初は③パレット単位で試行が開始された模様だが、ある加工食品メーカーの物流リーダーは、「パレット単位ではASN化しても検品が大変。だから基本的には1車単位から進めるべき」と語っている。同社は今、大手卸向け納品から順次、ASNを全国展開中である。このASN化の取り組みが他社にも、そして食品ほか産業界全体にも広がっていけば、「荷役等時間の削減」も有意に進展し、「運べなくなる物流危機」の回避に効果を発揮するはずだ。
結果として、過重な物流現場とドライバーの負担を取り除き、物流が「人間らしい、やりがいと尊厳のある仕事」になることを、筆者は心から期待している。
(つづく)
【Androidでドライバーの業務管理をDX化】
オカベマーキングシステムではドライバーの業務管理を円滑にする
業務用スマートフォン・タブレットなどのAndroidデバイスを販売しています。
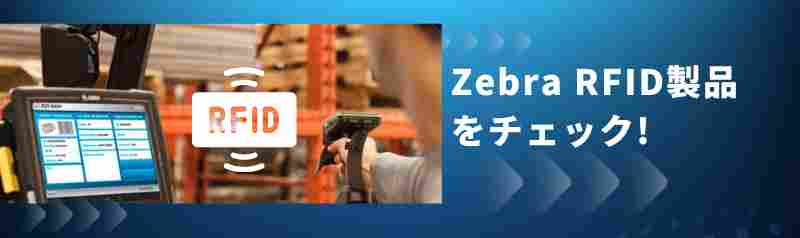